Why 3D MEP Models Are a Game Changer for Small Homes: Reducing Surprises and Slashing Costs
August 13, 2024 at 7:00 am,
No comments
In small residential projects, it’s quite common for detailed designs to focus primarily on architectural and structural elements, leaving the MEP (Mechanical, Electrical, and Plumbing) system routing for contractors to determine during construction. However, given the increasing complexity of MEP systems and the sheer number of components—pipes, lighting, mechanical equipment, maintenance areas, etc.—I believe it is crucial to include a detailed MEP design as well. But what about incorporating a 3D environment? Is there a significant advantage to creating 3D models for MEP systems in small residential projects? In this blog post, I will explore the benefits, including insights from my own experience with my house.
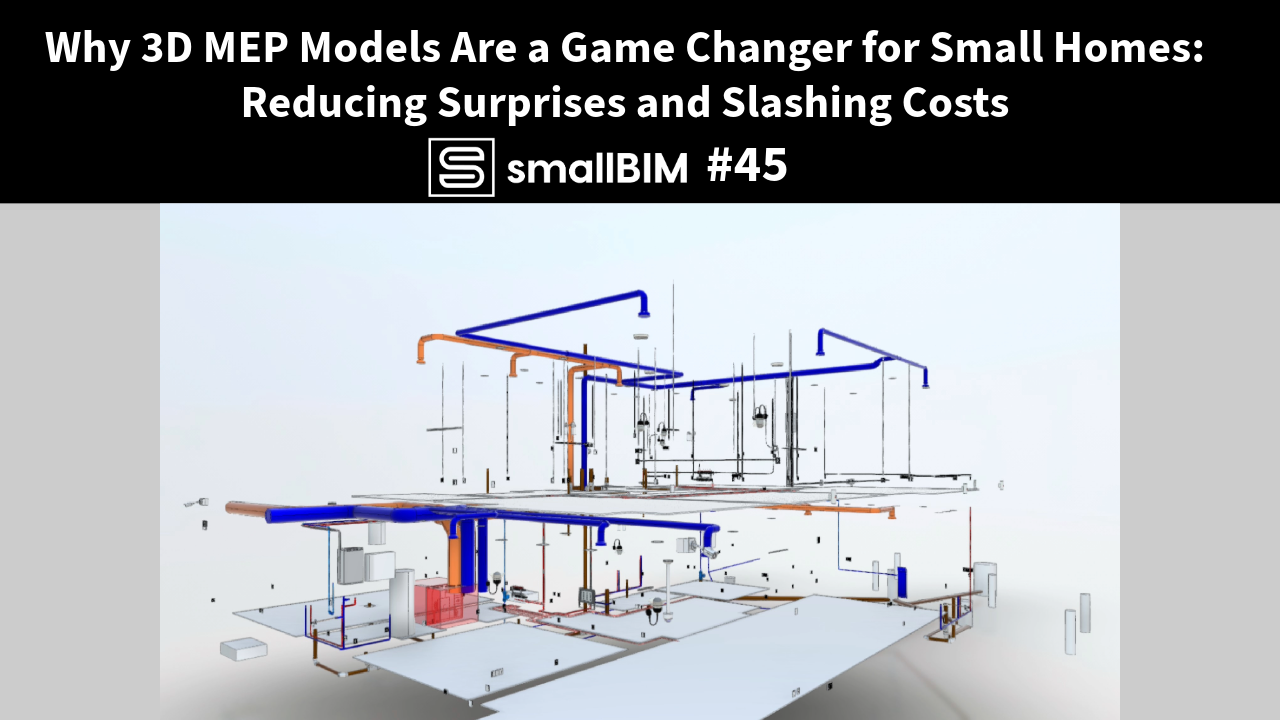
Elements and Complexity
It might be hard to imagine, but a modern house contains hundreds of meters of wires, pipes, ducts, and other components essential for comfortable living. Fitting all of these elements within a family home can be quite challenging. The image below shows the MEP model of my house, excluding the electrical wiring. Given this complexity, leaving all decision-making of MEP routing until the construction phase can be very risky.
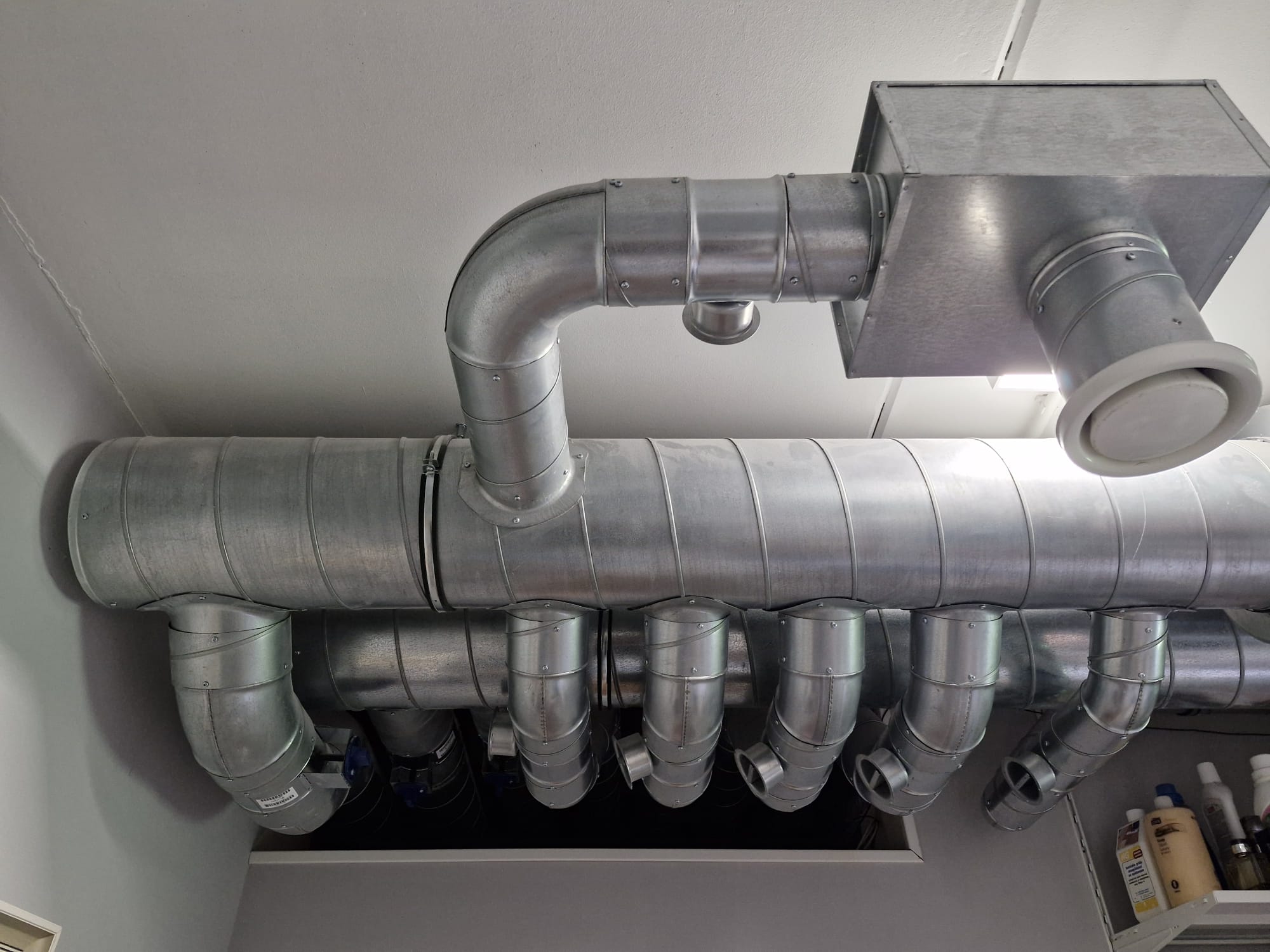
Picture: HVAC networks of my house
So having 3D models for all major disciplines, including MEP, can help you to visualize the systems better and see how they all fit together.
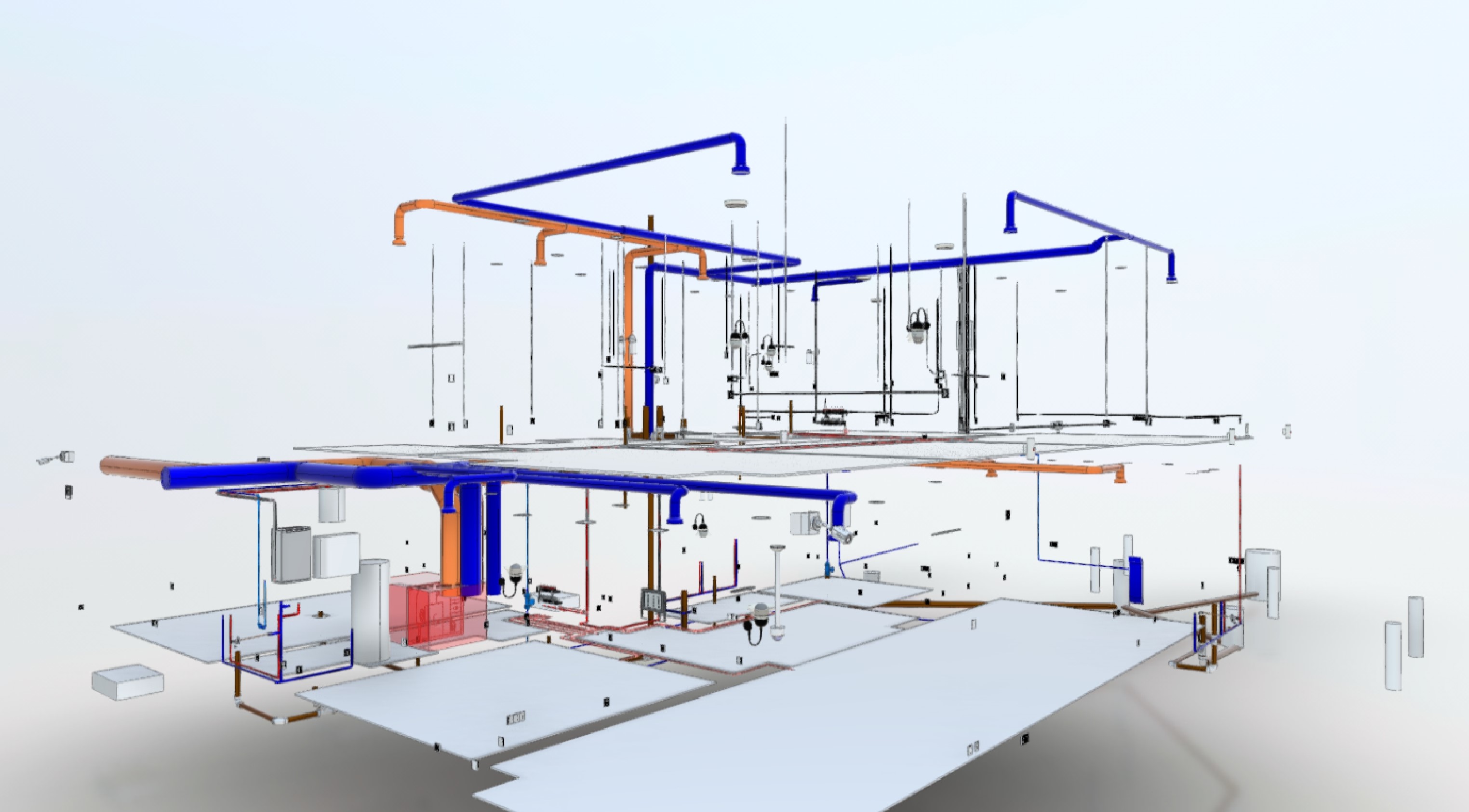
Picture: MEP 3D model of my house
Space Reservation
If you're installing a ventilation system in your home (which I believe is essential), proper coordination with the architectural, structural, and other MEP systems is crucial to avoid costly construction errors. Incorrect space reservations can lead to ceilings being lower than expected or pipes sticking out in undesirable locations.
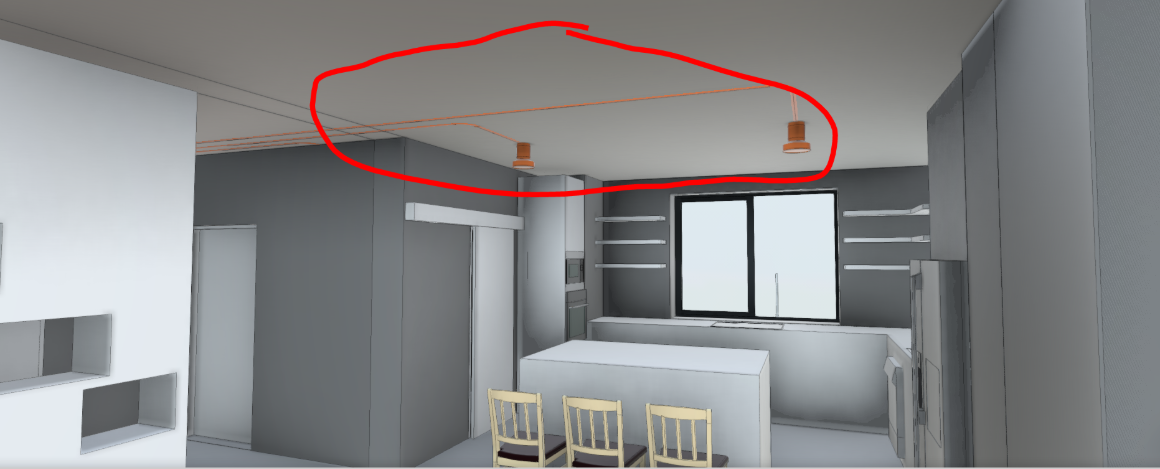
Picture: HVAC ducts not fitting under ceilings during design coordination.
Having 3D models allows you to visualize MEP routing options and provides other disciplines with a clearer understanding of what and where everything will be built. In my house, the HVAC routing revealed that the structural engineer needed to create a large opening in a load-bearing wall, leading to significant redesign. Had this issue been discovered during construction, it would have caused far more problems and increased costs.
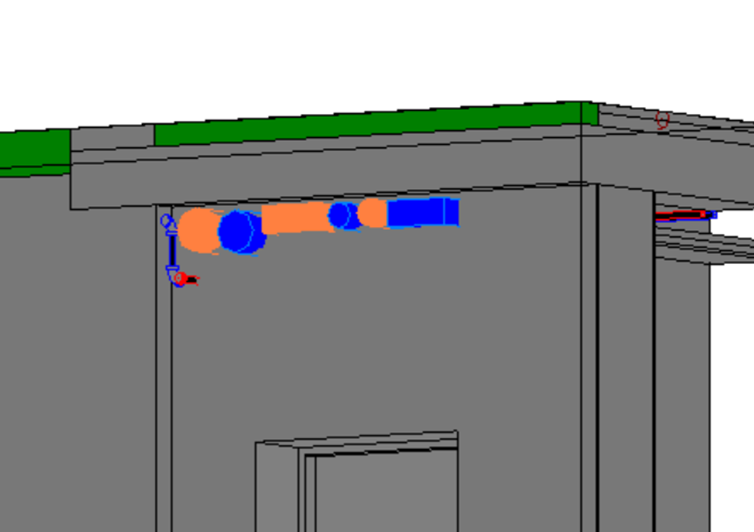
Picture: Missing opening for HVAC pipes during design coordination
Estimates
While wires, pipes, and ducts may not be the most expensive items in a house, their combined volume can significantly impact costs. If this volume isn’t properly accounted for, you may face unexpected expenses—for example, when the contractor informs you that additional funds are needed to cover all comfort requirements.
MEP models provide a much clearer understanding of these costs, helping you avoid surprises by offering more accurate quantity estimates.
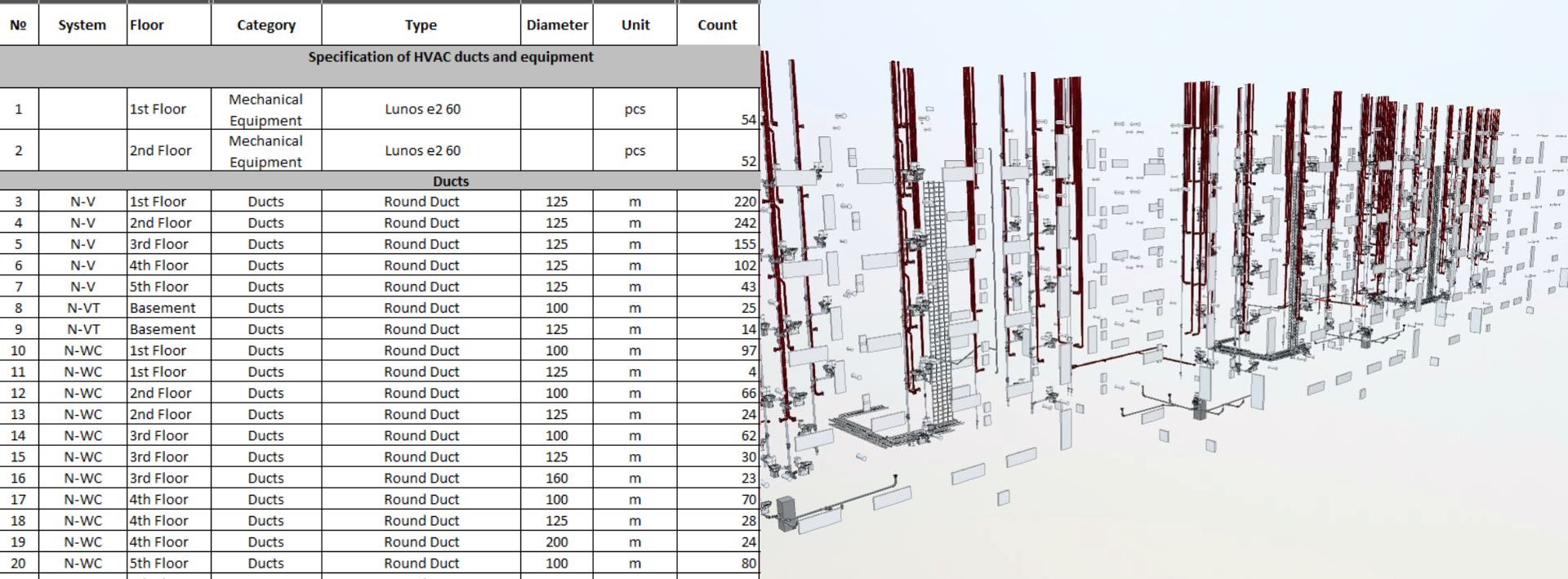
Picture: Automatic quantities extracted from building information models
Where to Get MEP models?
3D modeling of MEP systems is still quite uncommon for small residential projects, but there are several options if you're considering it:
- Hire a designer who can create 3D models.
This is the best option, though it can be the most expensive, in terms of initial investment. Having an engineer who can produce 3D models and generate accurate quantities and drawings from them is ideal for minimizing surprises during construction.
- Use a two-step approach: sketch and model.
You can have an engineer sketch your MEP system in 2D and then find someone to create a 3D model based on that sketch. I used this approach for my HVAC system: an engineer made a simple 2D sketch showing the pipe routing, and then I hired someone to model it. Platforms like Upwork or Fiverr can help you find freelancers for this task for a small fixed budget.
- Learn to create MEP models yourself.
If you have some engineering background, you could try creating the models yourself. However, this will require time to learn both basic MEP engineering principles and the necessary software, as well as obtaining the appropriate software licenses. You can start by simplifying and modeling only the major elements to see if everything fits together, possibly using simpler tools for this purpose.
Conclusion
While having 3D MEP models alone may not lead to significant construction cost savings, a fully coordinated design—free of major clashes—with drawings and quantities extracted from the models can result in substantial savings, potentially 10-20% or more of the total construction budget (SEE post). Creating these models or finding someone skilled in 3D modeling or BIM can be challenging, but in my experience, the return on investment is well worth the effort.