How pre-construction validation using BIM Can Prevent Cost Overruns and Design Errors in Construction
September 3, 2024 at 7:00 am,
No comments
Your building design is nearly complete, having been developed using traditional 2D methods. You’re either planning to tender for contractors or have already selected one, but construction has not yet begun or is still in the early stages.
Is there a way to reduce risks, such as cost increases or unpleasant design changes, that might arise from significant design errors at this stage?
Yes, there is—and Building Information Modeling (BIM) is one of the principles that can help, particularly in more complex projects, such as the reconstruction of existing buildings or the construction of new buildings with intricate shapes or functionalities. I refer to this process as "pre-construction validation," and during it issues related to blueprints, constructability and quantities can be identified. In this post, I will explore its principles and benefits.
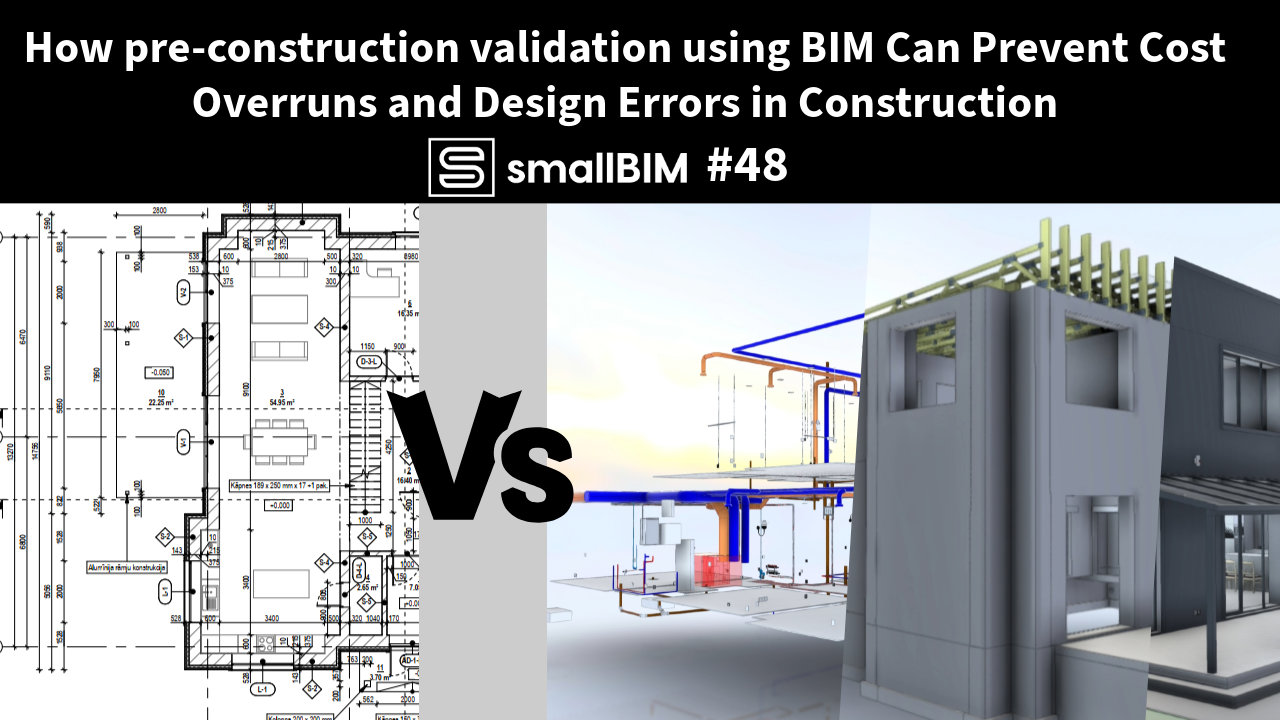
Models are Foundational
Pre-construction validation using BIM begins by creating 3D models, enriched with necessary information, from the 2D blueprints. This process allows for the early identification of potential issues. As a rule of thumb, if information is missing in the 2D drawings and poses challenges in creating accurate 3D models, it could likely lead to similar questions and complications during construction, such as "How should this be built?"
It's important to note that identifying major errors doesn't always require modeling every detail. For instance, modeling small plumbing pipes might be too time-consuming with limited added value, considering their low construction and material costs.
In my opinion, modelling major building elements such as walls, floors and major MEP elements is enough to identify the most significant issues.
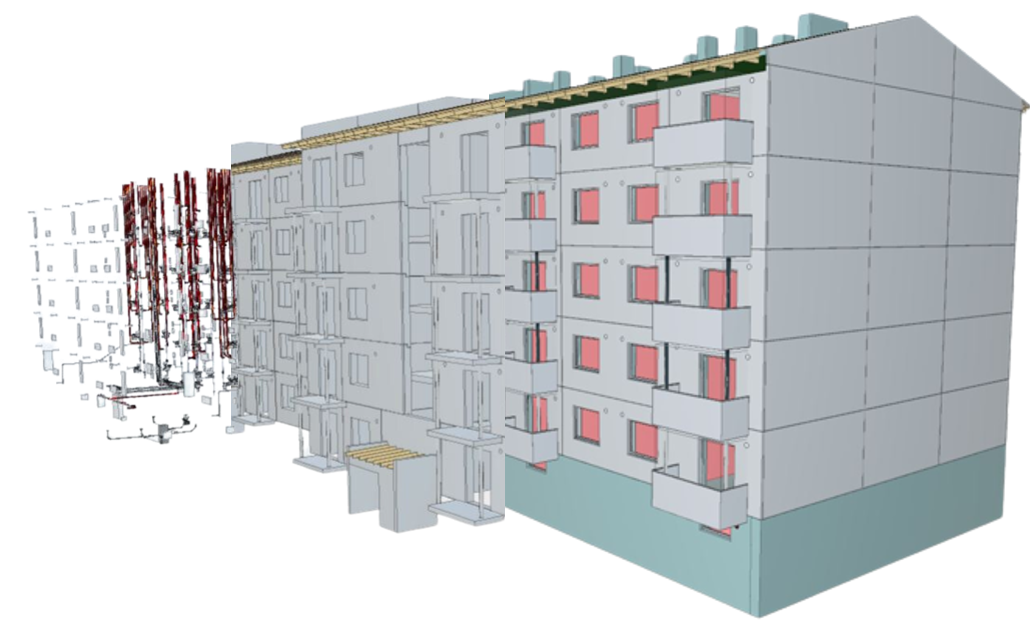
Simplified architectural, structural and MEP 3D models, containing only major elements to perform pre-construction validation.
Drawing Issues
In my personal experience, having been involved in more than a hundred construction projects, I have yet to see a project completed using traditional 2D methods without errors, even for the smallest buildings.
The pre-construction validation process can help identify common drawing issues such as:
- Missing Information: Elements may lack specified dimensions or other critical details.
- Misalignments: The same element may be located in different positions across different drawings. In simple terms, the element is shown in one place on one blueprint and in a different location on another.
- Information Mismatch: The size of an object might differ between the blueprint and the schedule or different blueprints.
- Construction Impossibilities: The provided information in the blueprints may not accurately reflect real-world conditions, making the element impossible to build (and model).
- Missing Drawings: It is quite common for some drawings to be missing altogether, such as details, sections, or entire systems. This forces the contractor to figure out how to fit the elements into the building from scratch.
Identified drawing issues, while created 3D models
Constructability
Constructability using BIM is a process where individual 3D models or combined models from different disciplines are used to determine if a design solution (and ultimately the building) can be successfully constructed. This is often where major errors made during the 2D design process come to light. Properly checking the alignment between disciplines, such as Architecture and MEP (Mechanical, Electrical, Plumbing), is nearly impossible in a 2D environment, leading to significant and costly errors discovered during construction. In some cases, these errors can even reduce the comfort and well-being of the building’s users.
With BIM, 3D models can be combined and checked to ensure everything fits together as planned. As mentioned earlier, not all objects need to be modeled to identify major issues. During this process, errors such as clashes between objects can be quickly and easily detected. Clashes typically indicate that objects are either incorrectly placed in relation to each other or that there isn’t enough space for them in the planned location. These clashes can also affect quantity calculations, as incorrect object placement leads to inaccurate quantities.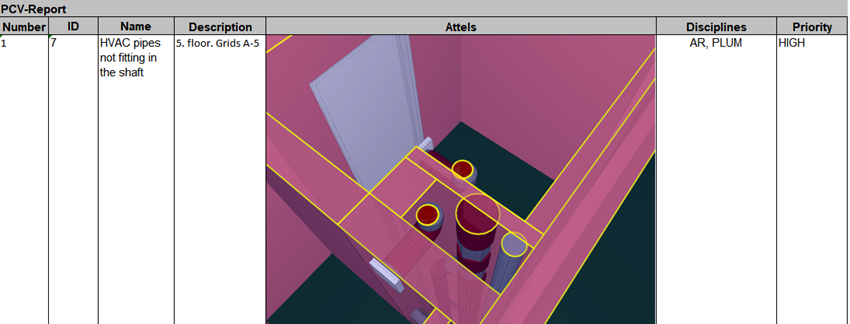
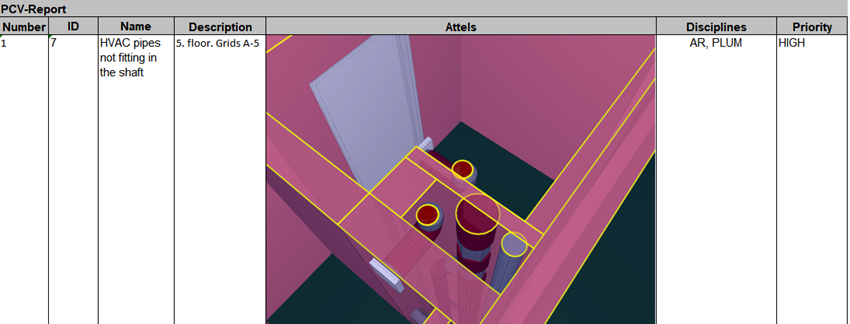
Identified constructability issues, be combining different discipline models. In this case pipes not fitting into shaft.
Quantity Comparison
Another valuable use case of BIM is reducing costly errors through quantity comparison. Quantities derived from BIM models are typically much more accurate than those calculated manually from 2D drawings. This data can be used to compare the actual quantities represented in the model to those calculated by designers, estimators, or contractors using 2D blueprints.
For example, when I was building my house, the estimator I hired used 2D drawings to calculate quantities. Although the design was created in 3D, significant errors were made in the estimates, which I identified by comparing them to the quantities derived from the BIM models. This comparison saved me thousands of dollars.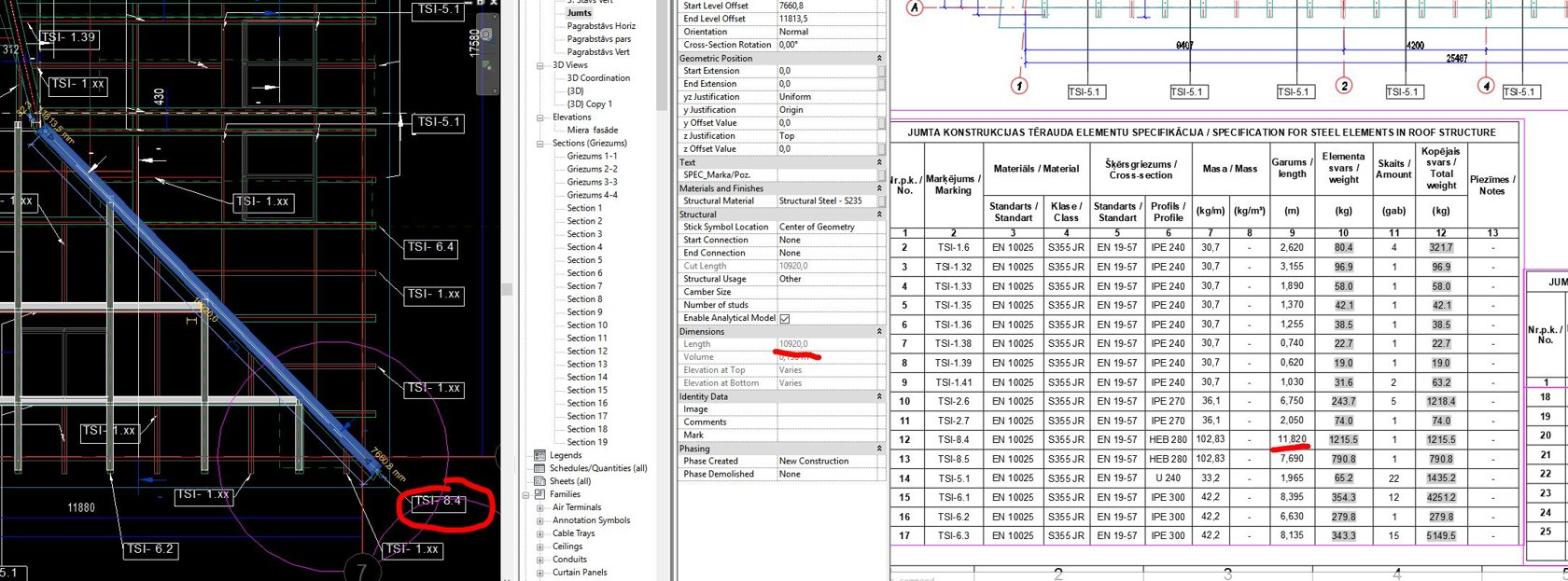
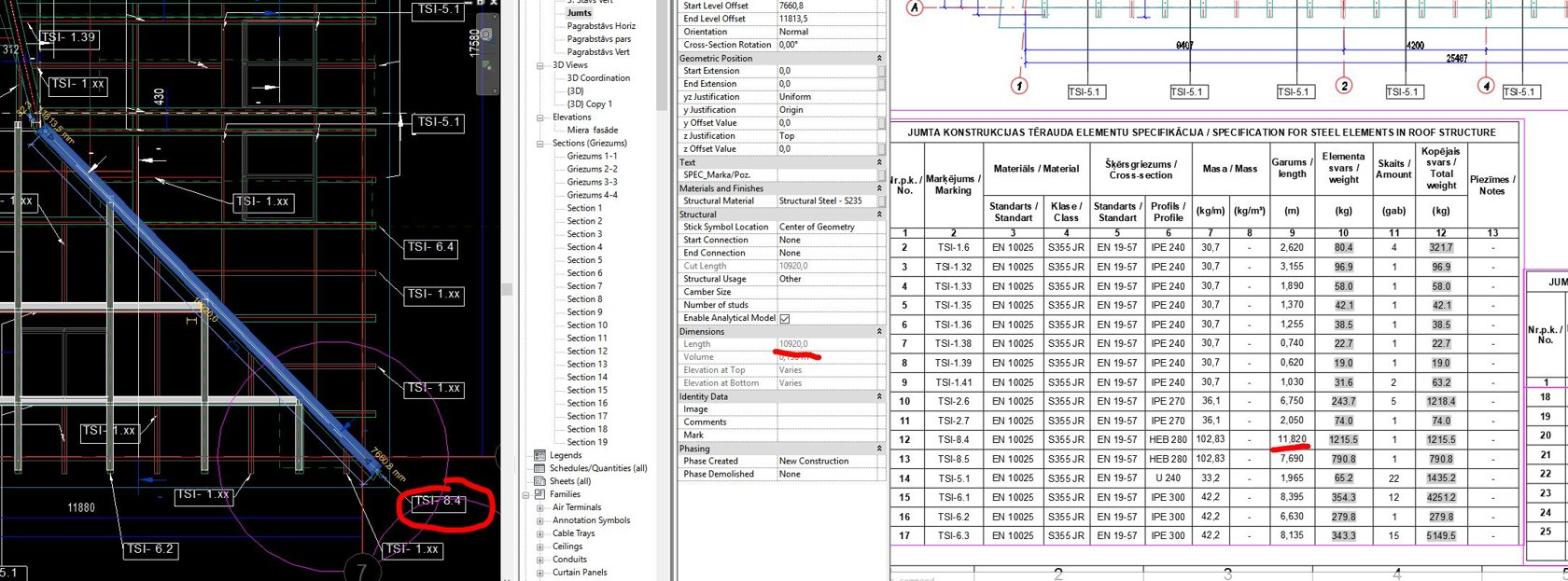
Quantities from BIMs are not the same as in 2D. Here a difference of 1m for a roof beam was identified.
Where to Start?
First and foremost, if possible, avoid designing in 2D altogether. The design costs for BIM-capable designers (at least in Latvia) can be comparable to those using traditional methods. Therefore, assembling a team that can work with BIM from the outset is far more advantageous than relying on pre-construction validation later.
If starting with BIM isn’t an option, you can turn to freelance designers or specialized companies like ITED to assist with the process. Creating BIM models from 2D blueprints is not easy—it can be labor-intensive and costly—but the benefits, particularly for the types of buildings mentioned earlier, can far outweigh these costs.
The speed of this process depends on the complexity and size of the building, but it typically takes a couple of weeks or more. This is an important factor to consider, especially if construction has already begun.
Conclusion
Utilizing pre-construction validation late in the design phase or early in construction can significantly reduce surprises and unexpected costs by identifying major errors and communicating them to the designers or contractors. Based on my personal experience and various case studies, these savings can range from 10-20% of construction costs, or even more. However, the most important benefit is that you won’t have to live with these errors for the next 20, 30, or more years while occupying the building.